In the fast-paced world of industrial manufacturing, efficiency is paramount. One often overlooked yet crucial component in textile production is the fabric rolling machine. Customizing these machines can significantly enhance operational efficiency, reduce waste, and improve overall productivity. This article delves into the myriad ways in which fabric rolling machine customization can revolutionize industrial settings.
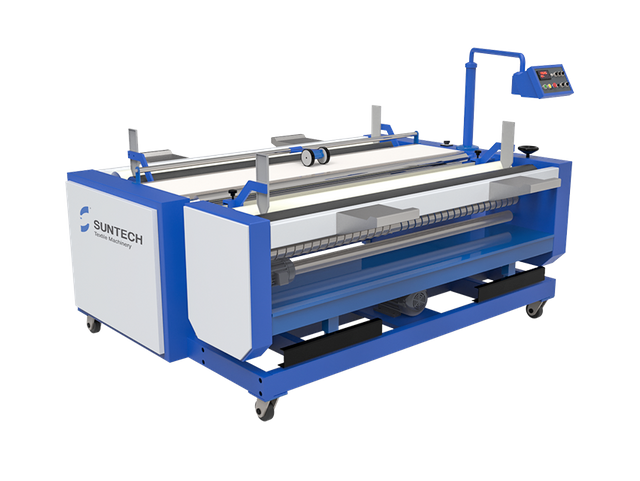
Understanding the Basics of Fabric Rolling Machines
Fabric rolling machines are essential in the textile industry, designed to roll fabric onto a core or tube for easy handling, storage, and transportation. These machines come in various configurations, each tailored to specific types of fabrics and production requirements. However, standard models may not always meet the unique needs of every industrial setting, which is where customization comes into play.
Enhancing Efficiency Through Customization
Customization of fabric rolling machines can lead to significant improvements in efficiency. By tailoring the machine to specific production needs, manufacturers can optimize the rolling process, minimize downtime, and reduce material waste. For instance, integrating advanced sensors and automation technologies can streamline operations, allowing for precise control over fabric tension and alignment.
Reducing Material Waste
One of the primary benefits of customizing fabric rolling machines is the reduction of material waste. Standard machines may not always handle delicate or specialty fabrics with the care they require, leading to damage and wastage. Customizing the machine to include features such as adjustable tension controls and specialized rollers can ensure that even the most delicate fabrics are rolled without damage, thus preserving material integrity and reducing waste.
Improving Productivity
Customized fabric rolling machines can also enhance productivity by reducing the time required for setup and changeovers. In a standard machine, adjusting settings for different fabric types can be time-consuming and prone to errors. Custom machines, however, can be designed with quick-change features and programmable settings, allowing operators to switch between different fabrics seamlessly. This not only saves time but also ensures consistent quality across different production runs.
Case Study: Customization in Action
Consider a textile manufacturer specializing in high-end, delicate fabrics. The standard fabric rolling machines they initially used resulted in frequent fabric damage and significant material waste. By customizing their machines to include adjustable tension controls, specialized rollers, and automated alignment systems, they were able to reduce fabric damage by 50% and increase overall production efficiency by 30%. This example illustrates the tangible benefits of machine customization in an industrial setting.
Conclusion
In conclusion, the customization of fabric rolling machines offers a powerful avenue for improving efficiency in industrial settings. By tailoring these machines to meet specific production needs, manufacturers can optimize their operations, reduce waste, and enhance productivity. As the textile industry continues to evolve, the importance of customized machinery will only grow, making it a critical consideration for any forward-thinking manufacturer.
Whether you are dealing with delicate fabrics or high-volume production, customized fabric rolling machines can provide the precision and efficiency needed to stay competitive in today's market. Embracing this approach can lead to significant operational improvements, ultimately driving success in the ever-evolving textile industry.